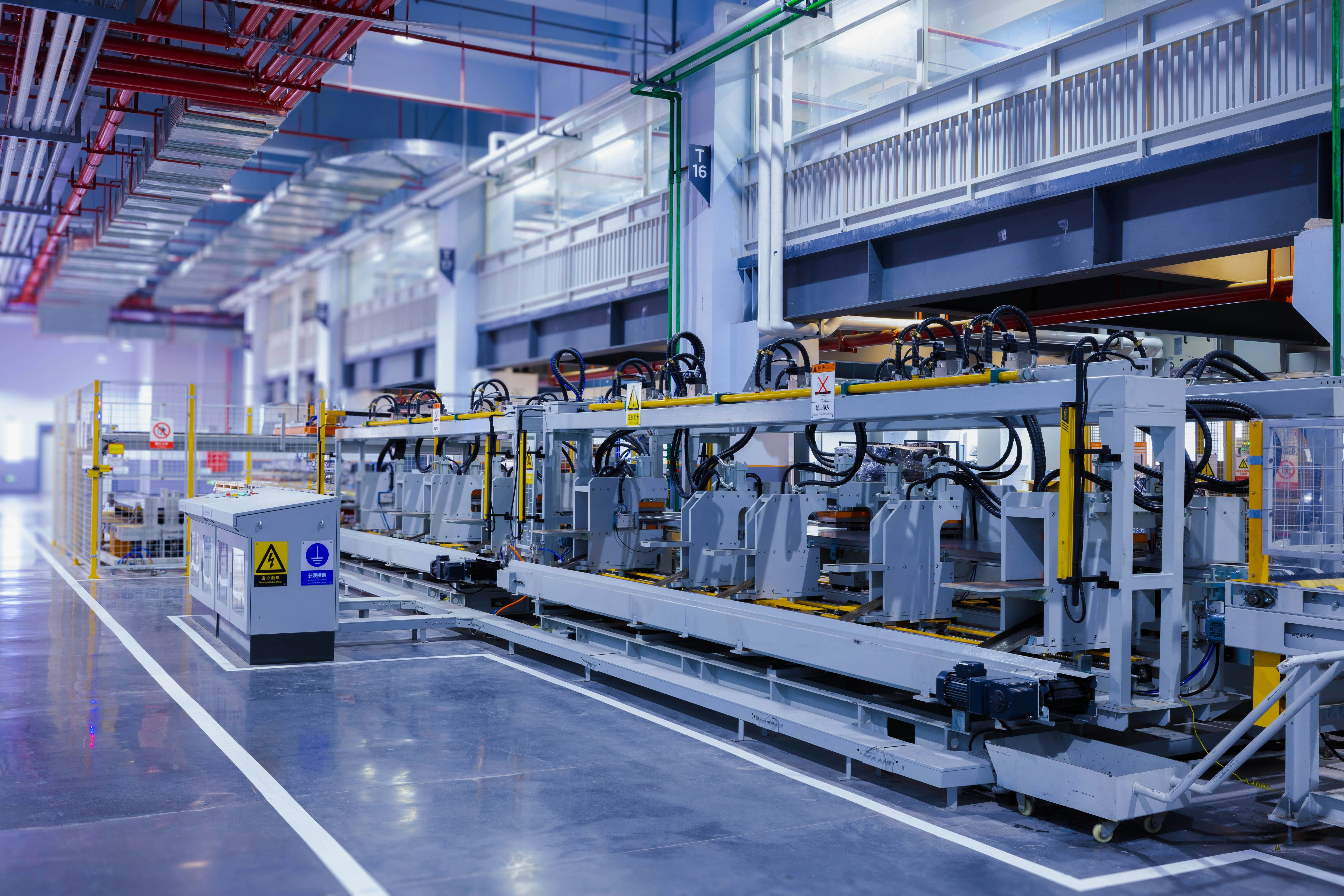
Process validation 101: Why your medical device needs to work (every single time)
This post was automatically translated from English. To see the original, use the language switcher at the top right.
TL;DR
(too lazy, didn’t read)
Process validation is basically making sure medical devices are manufactured consistently and safely, every time they're made. It's like having a foolproof recipe that guarantees your dish comes out perfect, except instead of a souffle, we're talking about life-saving medical equipment. This consists of ensuring that your manufacturing process has the right pieces installed, the right processes in place, and is tested for quality. In this post we break down what process validation is, why it matters, and how it actually works in the real world.
Introduction
If you order 10 pairs of scissors (don’t ask me why, maybe you’re in the paper cutting business), if one is faulty, that isn’t a big deal. You just let the seller know and you get a refund. Well.. imagine if you order 10 pacemakers you’re going to implant into 10 different people. If one of those is faulty, we have a big issue.
Enter process validation, the overlord of medical device manufacturing. It’s a systematic process of ensuring that your process you use for manufacturing has been validated so that every medical device produced by you comes out shiny, new, and working great.
According to industry statistics, process validation-related issues account for approximately 30% of medical device recalls, making it a critical focus area for manufacturers and regulators.
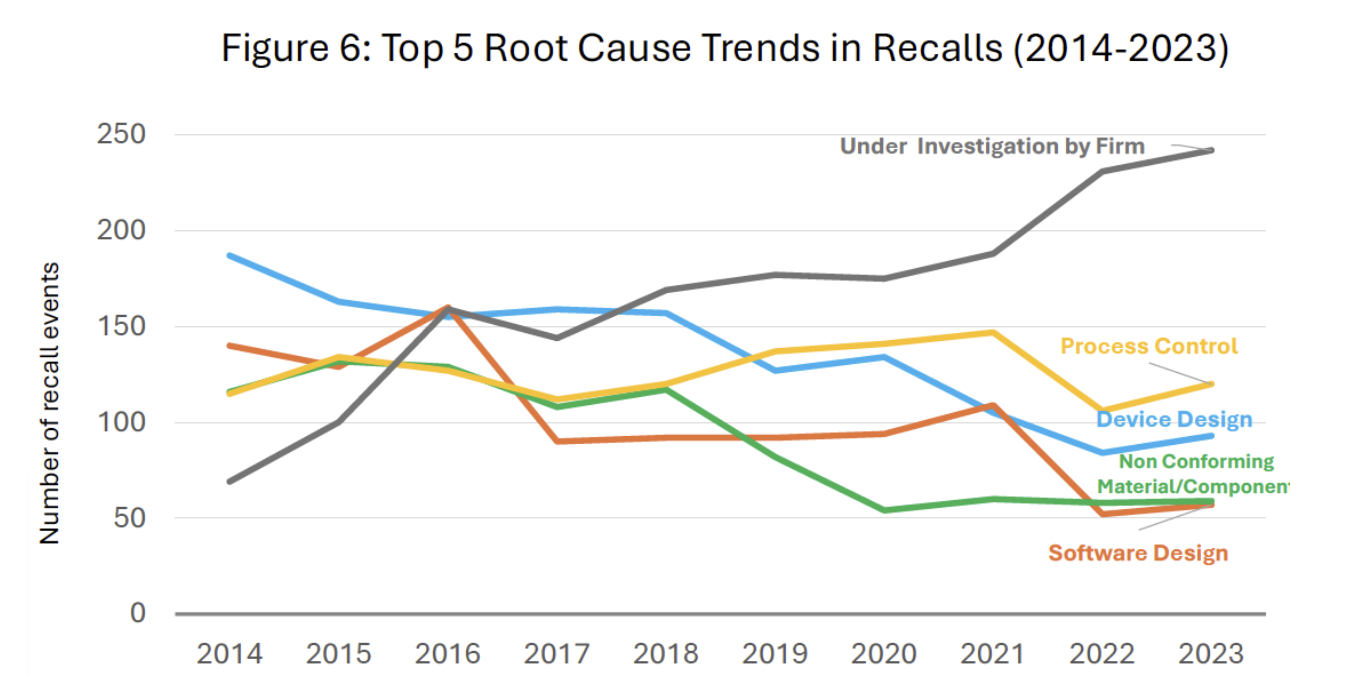
What is process validation?
In regulatory speak, process validation relates to processes whose output cannot be verified by subsequent monitoring or measurement. In normal speak, way to prove that a manufacturing process can consistently produce the same high-quality result, time after time.
Fun fact: The concept of process validation isn't new - it evolved from the pharmaceutical industry in the 1970s and has since become a cornerstone of medical device manufacturing. Today, it's referenced over 50 times in ISO 13485, the international standard for medical device quality management systems.
The Three Steps of Validation
Installation Qualification (IQ)
- Think of this as the "setup phase"
- Checks if equipment is installed correctly according to manufacturer specifications
- Includes verification of things like utility connections, calibration status, and safety features (basic setup)
- Typically involves documentation of equipment specifications and general installation requirements
Operational Qualification (OQ)
- The "stress test" phase
- Set the acceptable operating ranges (like temperature, pressure, etc.)
- Involves testing at both upper and lower operating limits
- Usually includes multiple test runs under various conditions
Performance Qualification (PQ)
- The final "consistency check" phase
- Makes sure the process works reliably under normal conditions
- Usually involves running multiple test batches of the device
- Focuses on reproducibility and consistency of results
- Typically requires statistical analysis of results
Real-World Application
Let's say you're manufacturing sterile syringes. The validation process would ensure that:
- The equipment is properly installed and calibrated
- The manufacturing process works within specific temperature and pressure ranges
- Every batch of syringes meets the same quality standards and comes out operational
- The sterilization process works, is consistent and effective on test syringes
Common Misconceptions
❌ "Process validation is a one-and-done process when I first start out"
✅ Actually needs regular review and updates, typically annually or bi-annually
❌ "Just run three batches and you're good"
✅ The number of test batches needs to be scientifically justified based on statistical significance. For low risk devices, maybe 3 is enough.
❌ "Old equipment doesn't need validation"
✅ Even existing processes need retrospective validation and periodic review
Practical Tips and Takeaways
For most startups and small companies, you will use a contract manufacturer for your products. In this case, get a contract manufacturer (CM) or supplier that is ISO 13485-certified since they’ve likely already validated their processes. This means:
- They’ve completed installation, operational, and performance qualification.
- They monitor and maintain their processes regularly.
- They can provide validation reports and process documentation upon request.
Additional things to do:
- Request and review their validation documentation to ensure compliance.
- Include audit rights in your supplier agreements to verify their processes.
- Leverage their existing validations, especially if they’re already producing similar devices.
- Ask for copies of this documentation to save as part of your quality management system documentation
Also, keep in mind you will need to do periodic surveillance of these manufacturers especially if they are producing your entire product or critical parts of it. Even when your subcontractor manages the process validation, you’re still responsible for compliance of your product. Make sure to:
- Request updated validation reports and process monitoring data annually.
- Communicate with the contractor so that if they make any significant process changes in their site, you’re aware of them.
- Watch for complaints or failures that might indicate the need for reevaluating the manufacturer process.
Conclusion
Process validation seems like (and is often) a lot of work, but it's incredibly important for ensuring medical devices are safe and effective. It is an investment in quality that pays off in patient safety and regulatory compliance.
Make sure you understand the process so you can make the right decisions when it comes to manufacturing. Best scenario - leverage a certified CM to handle most of that work for you so you don’t have to think about it too much.
Frequently Asked Questions
Process validation ensures that medical devices are consistently manufactured to meet quality and safety standards, reducing the risk of defects that could harm patients.
Yes. However, if using a contract manufacturer, startups should ensure the manufacturer is ISO 13485-certified and request their validation documentation, but they remain responsible for overall compliance.
Process validation should be reviewed regularly, typically annually or bi-annually, to account for any changes in equipment, materials, or regulatory requirements
Subscribe to Our Blog
Get notified for updates and new blog posts.